Launch of Eight Non-Financial Programs
In our new approach to materiality, Nippon Sanso Holdings specified 24 material issues, including three fundamental
preconditions for our existence, namely, respect for human rights, safety and security, and corporate ethics. To
address these
issues, we have created eight non-financial programs that will run across the entire group.
List of Non-Financial Programs
Non-financial programs |
Initiative |
E |
|
- Reduce our group's GHG emissions
- Reduce customer GHG emissions through environmental product offerings and applications
- Reduction in waste emissions
- Effective use of water resources
|
S |
|
- Reduction in lost-time injury rate, etc.
- Reduction in number of claims about products, offerings and applications
- Utilization of diverse talent
|
G |
|
- Compliance education and enforcement
|
Carbon Neutral ProgramⅠReduction of the Group’s GHG
emissions
Aiming for carbon neutrality in 2050
Realizing carbon neutrality through technological breakthroughs
Aiming to become carbon neutral by 2050, the NSHD Group aims to reduce its GHG emissions 18% by FYE2026 and 32% by
FYE2031. As shown below, our key initiatives to achieve these goals entail the replacement of air separation units
(ASUs), the purchase of green electricity certificates, and the introduction of renewable energy.
Further promotion of energy conservation and efficiency of energy use
- Replacement of air separation units (ASUs)
- Reduction of electricity usage through digital solution technologies
- Streamlining of logistics and review of transport
Promotion of the use of renewable energy and green power
- Switch to electricity companies with low emissions coefficients
- Purchase green power certificates
- Introduce renewable energy
Carbon capture and offsets
- Promote CO2 capture
- Carbon offset through new technology, forest conservation, and tree-planting activities, etc.
NSHD Group appropriately complies with climate change-related laws and regulations (in Japan, these include the "Act on the Rational Use of Energy and Conversion to Non-Fossil Energy Sources (Energy Conservation Act)" and the "Act on Promotion of Global Warming Countermeasures") and policies through various statutory reports to administrative agencies.
GHG Emission Reduction Targets
FYE2026: 18% reduction
FYE2031: 32% reduction (Base year: FYE2019)
Carbon Neutral ProgramⅡReduce customer GHG emissions through
environmental product offerings and applications
Through the NSHD Group’s products and services, we aim to achieve a reduction in GHG emissions that exceeds
the
Group’s own emissions.
The NSHD Group helps customers reduce their GHG emissions through the supply of its products and services. As a goal
for helping customers reduce their emissions, the Group is keen to achieve a reduction in GHG emissions that exceed
its own emissions.
Environmentally friendly products currently under development
- Oxygen-enriched combustion in blast furnaces
- H2 and NH3 combustion in industrial furnaces
- Carbon capture and utilization
(Lower customer GHG emissions through environmental product offerings and
applications)
> (Our group GHG emissions) (FYE2026)
Global GHG reduction through our products and technologies
Zero Waste ProgramReduction in waste emissions
We have set KPIs for our aims of securing water resources based on the regional and business characteristics of each
operating company.
Promoting the 3Rs (reduce, reuse, recycle) of waste processing is a requirement of our times. We will set and pursue KPIs for each operating company to reduce waste emissions and landfill volume. For example, in Japan, the Taiyo Nippon Sanso Group will work to halve its industrial waste landfill disposal by FYE2026 comparetd to FYE2019 under its Halve Amount of Landfill Disposal (HALD) initiative that was launched in FYE2022. Nippon Sanso Holdings is making steady progress toward achieving its targets by selling valuable materials in disposed high-pressure gas containers and by thoroughly separating and recycling waste, having achieved a 47% reduction in FYE2024.
Sustainable Water ProgramEffective use of water
resources
We have set KPIs for our aims of securing water resources based on the regional and business characteristics of each
operating company.
The NSHD Group strives to reduce water withdrawal by setting KPIs for each operating company in order to more
effectively use limited water resources. We surveyed water stress using the Aqueduct water risk evaluation tool
developed by the World Resource Institute (WRI) to identify manufacturing plants (ASU, HyCO sites) in high-risk areas.
At manufacturing plants in high-risk areas, we are taking steps to increase water recycling and reduce water withdrawal and consumption volumes.
Results of Water Stress Level Survey
The NSHD Group conducts a survey of water stress at all of its production sites in order to apprehend the risks
related to use of water resources and facilitate a more effective response to water risks. Using the Aqueduct water
risk assessment tool developed by the World Resources Institute, we surveyed water stress at 121 sites, with the
following results.
*Water risk category: Baseline water stress
Upper level: Water usage (thousand m3), lower level: Number of production sites
|
High |
High-medium |
Medium |
Medium-low |
Low |
Japan |
0 |
0 |
1,474 |
1,407 |
46 |
[0/20] |
[0/20] |
[8/20] |
[11/20] |
[1/20] |
United States |
997 |
2,028 |
1,979 |
820 |
2,123 |
[6/49] |
[11/49] |
[9/49] |
[8/49] |
[15/49] |
Europe |
3,816 |
0 |
6,013 |
0 |
15,859 |
[8/30] |
[0/30] |
[8/30] |
[0/30] |
[14/30] |
Asia and Oceania |
906 |
68 |
266 |
517 |
1,580 |
[7/20] |
[1/20] |
[2/20] |
[6/20] |
[4/20] |
Thermos |
0 |
0 |
48 |
0 |
120 |
[0/2] |
[0/2] |
[1/2] |
[0/2] |
[1/2] |
Total |
5,719 |
2,096 |
9,780 |
2,744 |
19,728 |
[21/121] |
[12/121] |
[28/121] |
[25/121] |
[35/121] |
- Data as of FYE2024
- Water stress survey conducted using Aqueduct water risk assessment tool
- Reporting boundary: Production sites with ASU, HyCO, or liquid carbon dioxide facilities with annual water
withdrawal of 20,000 m3 or more and Thermos
Safety First ProgramCultivating a culture of safety
Aim for world-class safety in the industrial gases industry
As a group that handles high-pressure gases, safety
is the foundation of our corporate existence. Guided by the mindset that “selling
gases is commensurate with selling safety,” we are dedicated to further promoting
safety and ensuring a safe and reliable supply of gases. As a Group KPI, we target
a lost-time injury rate (number of lost-time injuries per million work hours) of
1.6* or lower, and strive to be a global leader in safety.
*Target 40% reduction of average from FYE2017 to FYE2021 (2.53)
Specific measures to achieve goals
- Sharing information on workers’ and other accidents and best practices
- Improve safety capability by using DX, AI, and the IoT
- Safety education/utilizing the Technical Academy (foster a safety culture and improve sensitivityto danger)
- Investments in safety
Taiyo Nippon Sanso Corporation also takes the following measures for safety in addition to
reducing the lost-time
injury frequency rate:
- Reduce workplace accident rate
- Reduce the rate of vehicle accidents while transporting products
- Reduce the number of facility accidents
- CCPS assessment
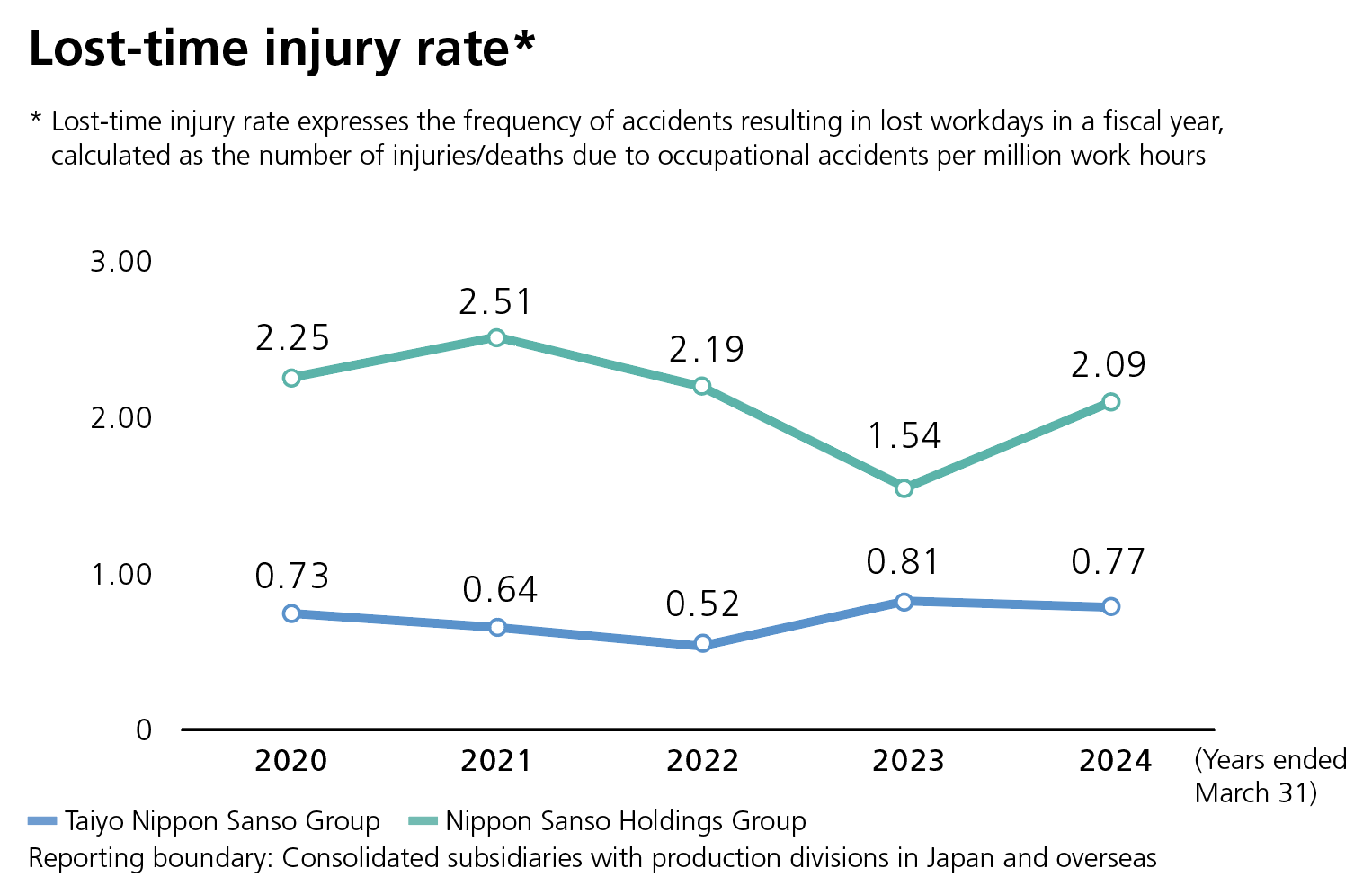
The lost time injury rate for FYE2024 decreased to 0.77 at Taiyo Nippon Sanso, but increased to 2.09 for the overall Nippon Sanso Holdings Group reflecting an increasing trend at other operating companies. Over the medium to long term, however, the rate is basically decreasing.
The above efforts have improved the lost-time injury rate to a level that meets the target.
Lost-time injury rate: 1.6 or lower (FYE2026)
Quality Reliability ProgramInitiatives for increasing
quality and reliability
Instilling corporate awareness of emphasis on quality and enhance quality and reliability of our group's products
As a corporate group dealing mainly in industrial
gases, we consider our unwavering quality commitment to be the stable supply of
products that underpin a range of industries, and that because our product is
an invisible gas, reliability is an essential quality that we must provide. We will
promote a culture that emphasizes quality by keeping our important promises to
customers and strive to further raise awareness among employees. We will also implement
a series of initiatives with the aim of increasing quality and reliability by
promoting the introduction of LIMS and other automation technologies.In FYE2024, the activities of the Quality Committee (SSG-QC) comprising the NSHD Group’s electronic materials gases manufacturing companies involved sharing best practices to increase customer satisfaction and discussing resolutions to issues. In the TNSC Group, we took measures to automate the sending of analysis data at our electronic materials specialty gas plant and promoted the introduction of quality control automation equipment at our chemical production plant. Furthermore, we continued our quality audit program* that began in FYE2023 and is being implemented across the entire NSHD Group.
*Each operating company conducts a
quality audit of their business sites once every three years based on important
audit items set by NSHD.
● Instilling quality-centric culture and improving awareness of employees
- Quality ethics and compliance education
- Quality audit program
- Share information on quality complaints along with measures for remediation and improvement
● Promote the introduction of LIMS and other automation technologies
- Automation of test, inspection, and analysis recording
● Increase satisfaction of electronic materials gases customers
- Increasing customer satisfaction through the activities of the Semiconductor Specialty Gas Quality Committee
(SSG-QC)
Talent Diversity ProgramIncrease human resource
diversification and engagement
Talent development strategies for sustainable growth
With an eye on sustainable growth, the NSHD Group intends to actively accept people of diverse talents, cultures, and
values, and to develop them as “The Gas Professionals.”
We have set KPIs related to empowering women and focus Groupwide efforts to achieve them. We encourage personnel
exchanges across regions in order to broaden their perspectives and grow while learning about each other’s
different
backgrounds.
Major initiatives to achieve KPIs
- Japan:
・Advance the Promotion Project Team for Women’s Active Engagement to the Diversity & Inclusion Office
・Formulated the Taiyo Nippon Sanso Declaration on Diversity and Inclusion to promote diversity and inclusion
- United States: Strengthen activities in recruitment marketing
- Europe:
WING (Women’s Ikigai Nippon Gases) Project (A human resource network comprising female employees for conducting women-centered events and training and promoting the presence of women)
- Asia and Oceania: Promote Unity in Diversity program
(educational activities for understanding different cultures, empowering women)
Initiatives for personnel exchanges
- Established task-based global teams that span regions (Example: Carbon Neutrality Promotion Project)
- Concept for a staff exchange program with operating companies
Rate of female employees |
FYE2026 ≧ 22% |
FYE2031 ≧ 25% |
Rate of female management posts |
FYE2026 ≧ 18% |
FYE2031 ≧ 22% |
Compliance Penetration ProgramCompliance penetration
and enforcement
Compliance training at all operating companies
The NSHD Group positions respect for human rights, safety and security, and corporate ethics as preconditions for its corporate existence. Each operating company offers various compliance training courses aimed at getting employees to expand their awareness of compliance and acquire correct knowledge. With a shared understanding that ensuring all employees take compliance training is the basis for establishing compliance, we have set a 100%* rate of receiving compliance training as one of the non-financial KPIs in our medium-term management plan.
*Applies to mandatory “main training” for all employees in each region
Compliance training result (FYE2024)
99.4%(
100% completion rate as of the end of June 2024)
Region |
Main training and themes |
Japan |
Explanation of compliance, harassment prevention, respect for human rights, observation of antimonopoly laws, and whistleblowing |
North America |
Code of Conduct, employee core competency (workplace ethics and compliance initiatives), and harassment prevention |
Europe |
Code of Conduct |
Southeast Asia and India |
Code of Conduct, explanation of compliance, bribery and corruption prevention, and whistleblowing |
East Asia |
Code of Conduct, workplace harassment, conflict of interest, corruption prevention, personal data protection, and whistleblowing |
Australia |
Code of Conduct, awareness of fraud, workplace bullying, harassment, and discrimination |
Taiwan |
Code of Conduct, ensuring a respective workplace (harassment), and personal information protection |
Rate of receiving compliance training: 100% (FYE2026)